- Published 19 Apr 2024
- Last Modified 19 Apr 2024
- 7 min
Power Module Failure Analysis
Power modules are industry workhorses that are also proving crucial to the energy transition. Read our guide to discover the types of power modules on the market and how to prevent power modules from failing.
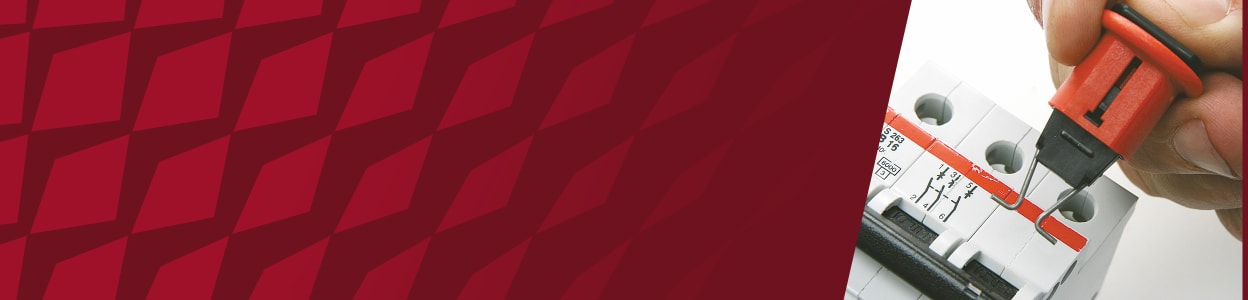
Reviewed by Stavros Skourakis, Technical Support Engineer (March 2024)
Power modules are used in a wide range ofelectronic solutionsand applications, from electric vehicles to renewable energy. Read on to find out more about the different types of power modules on the market, what they are used for, why power modules sometimes fail, and how to maintain them correctly. We’ll also take a look at the future of the power module market.
What are Power Modules?

But first, just what is a power module? Power modules contain several power semiconductor devices, which are widely used in industrial drives and motors, uninterruptible and AC-DC power supplies, and power inverter applications for renewable energy sources such as solar and wind farms. The power module typically houses power semiconductors such as MOSFET, IGBT, thyristor, JFET, BJT or rectifier diodes in a robust and tightly integrated package specifically designed for power conversion.
Power modules reduce parasitic capacitance and inductance effects in a circuit – elements that adversely affect circuit performance – and typically feature thermal management such as a heat sink to remove heat generated during power conversion. Power modules act as building blocks in electronics design, providing engineers with carefully specified, integrated components that are suited to applications where high levels of power control are used. Due to the heat that builds up in power modules, effective thermal management is important to prevent their failure.
Types of Power Module
There are several types of power modules available. Common power module types include:
- Insulated gate bipolar transistor (IGBT) power modules. These semiconductors are used as switches to prevent or enable power flow. They are employed in industrial motor drives, electric cars, trains, and solar inverters as well as uninterruptible power supplies and energy storage systems. IGBT power modules convert electricity from one form to another, for example from AC to DC power
- Metal oxide semiconductor field effect transistor (MOSFET) power modules. MOSFETs are a very commonly used type of transistor. MOSFET power modules are used to control current in power electronic circuits. They require almost no input current to control the load current. MOSFETs are designed for switching applications. They are used in automotive motors and charging applications
- Intelligent power modules. Intelligent power modules provide robust and simple control and protection to optimise performance. The module is based on a three-phase inverter circuit with a power management controller that contains a gate driving circuit and protection components. It is easier to design power management circuits with an intelligent power module than it is with conventional IGBT modules
- Silicon carbide modules. These modules include silicon carbide MOSFETs and silicon carbide diodes. They are used in solar inverters in the DC-DC stage. Silicon carbide is used as a semiconductor because of its high efficiency and ability to operate at high temperatures and voltages compared to conventional silicon
- Silicon / silicon carbide hybrid modules. These power modules combine silicon diodes, IGBTs, and silicon carbide diodes. Solar inverters use these types of power modules to convert DC into AC power. They are also widely used in uninterruptible power supplies and energy storage systems
IGBT Power Modules
IGBT power modules have several qualities that have seen them become the predominant power module in industry. They are used to switch electrical power on and off very quickly, with high levels of efficiency and good temperature performance. The module typically consists of IGBTs in electrical configurations including half-bridge, chopper, booster, sixpack, and other layouts.
IGBT inverters are often used to convert electricity from renewable energy into power for the grid. IGBT inverters are also widely used to convert the electricity from electric vehicle batteries from DC to AC, driving the EV’s motors.
Power Module Applications
As well as inverters, power supplies, industrial motor drives, and transportation, there is an array of other power module applications, including:
- Medical electronics
- Appliances
- Welding equipment
- Battery charging
- Heating, ventilation, and air conditioning system controls
- Electroplating equipment
- Elevators
- Water pumps
Power Module Failure
Power control modules can fail for a variety of reasons. They may fail because they overheat, overcurrent, or voltage spikes. One common cause of failure is mismatches between the coefficients of thermal expansion (CTE) within the module that lead to solder fatigue, stressed components, cracking, or fracture of brittle materials such as silicon. There are many different causes of voltage surges and spikes.
Thermal Management
This means thermal management is an important aspect of stabilising heat dissipation and effectively preventing power modules reaching very high temperatures, which leads to component failure. It’s crucial to manage the heat generated within the power IGBT module so it doesn’t affect operations.
Why Do Power Modules Fail?
Indeed, thermal management may well be the single most important factor in preventing the need for power module repair. A power electronics module should be designed to remove the heat that builds up during its operation as efficiently as possible. If the power module components are allowed to heat up, their long-term reliability suffers. Surfaces that are soldered together but have different CTEs will experience mechanical stress, which can lead to cracks in the solder – and ultimately the failure of the device.
Power Module Analysis
Failure analysis of power modules shows most failures take place soon after installation – because of manufacturing defects or incorrect installation. Testing can be carried out to help predict failure and understand the impact on a particular type of module of many cycles of usage. For example, accelerated power cycling in a test environment helps engineers determine the likelihood of failure when a power module is subjected to continual electrical loads. This also helps engineers understand the performance of solder joints and thermo-mechanical stresses within the power module.
Power Module Maintenance
Always remember that power modules can be hazardous if not operated and maintained correctly. Maintenance should only be carried out by authorised engineers or technicians from the manufacturer. Power module maintenance, including removing dust and any other contaminants, should be undertaken at regular intervals. Cables should be checked for corrosion or damage and replaced if necessary. Frequently checking the power module’s ventilation system is essential, as overheating of the power module can cause unforeseen failures. If replacing electronics module components, ensure that all screws and fixtures within the power module casing are tightened correctly.
Power Modules in the Future
Globally, the power module market is growing fast because of the increasing use of electric vehicles and the integration of renewable energy resources onto the grid. MOSFET and IGBT power modules have become the market-leading type of power conversion in recent years and the development of new, even higher-power current output designs of power modules is a key technology future trend. Applications include renewable energy and power transmission.
There are also new high-temperature silicon carbide power modules coming onto the market. These types of modules overcome some of the problems related to differing coefficients of thermal expansion and resulting in thermal-mechanical stresses.
For electric vehicles, more sophisticated designs of power modules are helping achieve higher power density in applications such as converting battery power into three-phase alternating current (AC) to drive the vehicle’s propulsion system. Gallium nitride transistor-based power modules are expected to help enable the next generation of electric vehicles by reducing the size, weight and cost of drivetrains.
So, power modules are not only staples of an industry, they are also proving crucial in the energy transition. That means their importance as a means of power conversion and energy transition is only set to grow in the coming decades as the Better World products continue to decarbonise the economy.
Do you need a power module for your application? RS can help. Check out our range of IGBT modules.