- Published 24 Apr 2024
- Last Modified 24 Apr 2024
- 6 min
The Future of OEM: Industry Trends
Changes in technology and customer needs will drive a whole new future for original equipment manufacturers. Find out more about the future of OEM in this article.
/OEM_5120_x_600.jpg)
Reviewed by Stephen Bettles, Technical Support Engineer (April 2024)
The future of OEM is leaning towards increased adoption of the technology and software of the Fourth Industrial Revolution, or Industry 4.0. This means extensive machine interconnectivity, increased OEM automation, and controlling manufacturing processes through AI and other OEM software. This guide will present manufacturing industry trends and the high-tech features of the future of manufacturing.
What Will Be the Impact of Technology on Manufacturing?
Technology has shaken up manufacturing throughout all the industrial revolutions. From steam engines to assembly lines to computers to interconnectivity, advances in machines have advanced how machines get made.
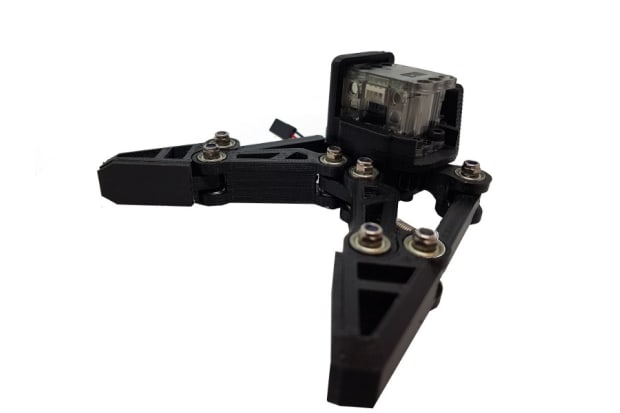
This continues today through the Industrial Internet of Things (IIoT). Today’s manufacturing machines can use sensors to broadcast their operating conditions to (and receive instruction from) OEM software like AI, a CMMS, and digital twins. PLCs, though no less vital today, are not the only game in town for monitoring and controlling equipment. Manufacturing technologies allow incredible levels of control and synchronisation, but this takes careful planning and testing to reap optimised production.
Industry 4.0 also extends to automation and robotics. Industrial robots can manage more and more manufacturing tasks, but humans are also finding new roles in this future through cobots - robots that work alongside humans to handle dangerous or repetitive tasks while humans focus on the work requiring intuition and creativity.
What Will Be Driving Manufacturing Industry Trends in the Future?
Manufacturing industry trends will see original equipment manufacturing innovations in hardware, software, and sustainability shape an interconnected future of manufacturing.
Digital Technology
OEM software is rapidly advancing using Industry 4.0 innovations, bringing digital technology front and centre in the future of OEM.
Smart inventory systems, including computerised maintenance management systems (CMMS), provide greater control and planning of these necessary OEM business costs. A CMMS can plan stock levels based on actual expected business needs and coordinate purchase orders and picking around jobs. This reduces stock levels and their inherent tied-up capital and operating costs. This OEM software can also plan machine maintenance based on operating conditions or fixed schedules.
Artificial intelligence is permeating our lives, and this includes original equipment manufacturing technology. AI can predict required maintenance, spot quality defects invisible to the human eye, identify trends within reams of data, and optimise scheduling. The future of manufacturing stands to see AI play a large role.
IIoT devices and cloud computing allow the monitoring and controlling of manufacturing processes from anywhere. This allows checking on different branches of your company from anywhere in the world but also lets operators on the floor receive machine updates and alerts on their smartphones.
Predictive Maintenance
As original equipment manufacturing technology increasingly connects to other machines and broader systems, remote maintenance management systems can predict what care machines need.
Predictive maintenance collects and analyses data from IIoT-enabled machines to detect developing problems. Vibration sensors are a chief example since irregularities they detect are often difficult issues to address. AI in OEM software can raise alerts about potential problems, allowing manufacturers to proactively shut down equipment for maintenance accordingly. This allows detecting and mitigating issues far earlier than was possible before, which in turn prolongs equipment life, avoids downtime, and maximises investment returns.
Operational Efficiency
Industry 4.0 innovations extend throughout manufacturing technologies, creating improvements in operational efficiency:
- Minimised human error through widespread OEM automation and industrial robots
- Efficient energy usage due to OEM software determining and maintaining process parameters’ ideal conditions
- Faster processes and greater production output from OEM and automation synergies
- Rapid prototyping design stages using 3D printing
- Optimised supply chain achieved through RFID tags and blockchain technologies tracking product journeys
- Reduced material waste thanks to predictive maintenance calling for filters and lubricants only when required
Smart Manufacturing
As with predictive maintenance, smart manufacturing uses sensors in IIoT manufacturing devices to detect deviations from ideal operation. Smart manufacturing seeks to actively optimise manufacturing processes, though, rather than call for shutting them down (though balancing both areas will be key for the future of OEM).
Smart manufacturing can adjust OEM automation to maximise its output. It can also analyse and present trends in operating conditions, allowing manufacturing engineers to spot system inefficiencies. This can include wasteful use of materials, choke points in production, or areas of high heat generation.
Smart manufacturing can also extend to automatically ordering raw materials based on production needs, assigning manufacturing equipment to jobs, and planning batches’ distribution.
/By%20Your%20Side/smart-factory.jpg)
Real Time Information
The constant, widespread connectivity of the Industrial Internet of Things makes real-time information a key part of the future of OEM.
Digital twins use data from IIoT devices to create real-time, ongoing simulations of manufacturing machines — or even of manufacturing plants or entire supply chains. With a digital twin of a physical manufacturing process, you can monitor operations, simulate scenarios, predict future issues, and evaluate the manufacturability of new products. Digital twins improve your understanding of your operations and help you identify your constraints.
Real-time supply chain management is more extensive thanks to innovations like RFID tags and blockchain. These tags allow an ongoing log of material info, and they allow scanning at every point in the manufacturing process: This can include the journey from the supplier, storage in the OEM’s inventory, the manufacturing process itself, and the trip to the end user. With this knowledge at your disposal, you gain reduced uncertainty and can pinpoint weaknesses in your supply chain.
What Will This Mean for OEMs?
As with all technological advances, the people and businesses who embrace them will find a firm footing in the future. The future of OEM will see companies thoughtfully assessing which aspects of Industry 4.0 suit their business and can provide true benefits — always a better approach than just jumping in headfirst to follow the latest trend.
This can mean:
- Analysing business challenges, constraints, and loss sources to see where AI or other original equipment manufacturing innovations could help
- Determining which equipment conditions truly need monitoring (and the capital investment of sensors and computing capacity)
- Factoring in the ongoing costs of new technologies: training, electricity, computing power, software licences, data storage, cooling, troubleshooting
- Strengthening cybersecurity to prevent the IIoT’s connections from compromising security
- Finding ways for people to find meaningful work alongside cobots — and keeping safety front-of-mind
- Considering whether the business’ customers would like access to the sustainability transparency Industry 4.0 enables
RS can help you learn about Industrial IoT Solutions and how they can be a part of your place in the future of OEM.